Fibre Extrusion Technology Limited
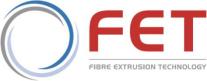
Address
Fibre Extrusion Technology Limited
Gelderd Road Unit F & G, Treefield Industrial Estate
Gildersome, Morley
LS27 7JU
Great Britain and Northern Ireland
Telephone+44 113 253 7676
Discover more from us
About us
FET designs, develops and manufactures bespoke extrusion equipment in Laboratory, Pilot or Production scale for a wide range of high value textile material applications worldwide.
“Innovative Fibre Solutions”
Introduction
Fibre Extrusion Technology Limited (FET) was established in 1998 with the firm objective of achieving technical excellence in our field and helping customers to efficiently produce high value textile materials. The company designs, develops and manufactures bespoke extrusion equipment in Laboratory, Pilot or Production scale for a wide range of high value textile material applications worldwide.
Our customers tell us that, much more than just a supplier, they need the services of a true partner to succeed – one with comprehensive experience, knowhow and a proven track record, working with some of the world’s foremost technological innovators.
Managing Director, Richard Slack explains where FET’s main strength lies. “In particular FET excels at finding solutions where others cannot. New Product Development and R&D departments often approach us with unique challenges related to man-made fibre and yarn extrusion issues. We are proud to have an extremely high success rate in achieving solutions”.
Major products
- The FET-100 Series is the mainstay of the FET range of meltspinning products, offering considerable flexibility with interchangeable production formats, such as Multifilament, Nonwoven and Monofilament.
- Where melt spinning solutions cannot succeed, FET provides a viable alternative with pilot and small scale production FET-200 Wet Spinning Systems. Also available are vertical wet spinning and dry jet wet spinning versions.
- The latest addition to FET’s product portfolio is the FET Spunbond Nonwoven system, a technical variation on the meltspinning process, which can enable fibre properties such as absorbency, washability and liquid repellence.
- Spunbond can also be twinned with meltspun technology to enable Composite nonwoven systems, where specific properties can be combined.
The FET Fibre Development Centre
Following a large investment programme, the Fibre Development Centre opened in 2023. Customers now benefit from an enhanced process development laboratory and support facilities for client testing and product development, specifically designed to make their stay more efficient and comfortable. Ample meeting room and office space in this building has freed up over 50% additional capacity for design, production and other facilities elsewhere.
Typical examples of materials tested at the Fibre Development Centre include biomedical materials; specialized novel fibres; sustainable polymers; biodegradable and composting materials; textiles for a wide range of composites; functional textile materials; and non-woven materials from viscous polymers.
Sustainability
Our principle theme at Techtextil is Sustainability. FET systems are ideally suited for both process and end-product development of sustainable materials, enabling customers to undertake their own process development in-house.
With installations in over 35 countries, FET is geared to working within the global marketplace and with diverse cultures.
Our product groups
Our application areas / Solutions
Downloads
Keywords
- Pilot and Laboratory Fibre extrusion equipment
- Meltspinning systems - Monofilaments and Multifilaments
- Wet/Gel spinning systems - Monofilaments and Multifilaments
- Fiber Development and Process Development Services
- Meltblown and Spunbond systems for Nonwovens
Our Products
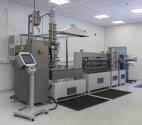
FET-200 Series
Pilot & small scale production wet spinning systems
Where melt spinning solutions cannot succeed, FET provides a viable alternative with pilot and small scale production FET-200 Wet Spinning Systems. These may be used for a variety of solvent and polymer combinations:
- Wet spinning for processing new functional textile materials
- Allows maximisation of polymer and hence fibre properties
- Optimisation of process conditions for transfer to large scale
- Small scale production for bespoke high value products
- Available for multifilament, monofilament and staple fibre formats
The FET-200 Series is available for multifilament, monofilament and fibre in both laboratory and pilot scale. With many high performance applications, such as biomedical and composites, these systems are proven and successfully operating worldwide.
FET-200 Features and Benefits:
- Single or multiple dope vessels of various sizes for batch / continuous operation
- Continuous homogenization of spin dope with temperature control
- Exchangeable precision spin pumps and height adjustable spin engine
- Horizontal, vertical spinning in the coagulation bath, with unique thread-up system
- Temperature control of coagulation and solvent recovery
- Highly efficient washing haul-off systems
- Numerous combinations of washing baths available
- Filament drying systems with hot air circulation
- Flexible configuration of draw line components with multiple drawing zones
- State of the art computerised control system with data acquisition
Dry-jet wet spinning method
This method, also known as gel spinning, is an alternative to wet spinning. Some fibres, when spun directing into the bath, may create micro-voids that negatively affect the fibre properties. The polymer is dissolved in a solvent to make the fibre solution, which is then extruded under heat and pressure into an air gap before it enters a coagulation bath. The produced fibre is then washed and dried before it is heat treated and drawn. This method is often required for high performance fibres with a liquid crystal structure
Vertical wet spinning method
In the past, wet spinning has always been conducted by submersing the spinneret into the solution and conducting the extrusion horizontally. However, at FET, we have recently developed a vertical spinning system. This line utilises the Venturi effect to allow for better exposure of coagulation media with the dope and easier threading up of the yarn. This is particularly useful when working with more challenging coagulation solutions such as concentrated sulphuric acid or highly basic solutions.
All FET-200 Wet spinning systems are tailor made and take into account required throughput polymer/solvent combination and downstream process conditions.
FET-200 LAB
Laboratory scale wet spinning systems
In addition to pilot and small scale wet spinning production lines, FET now also designs and manufactures a lab scale version which is more suitable for the early stages of formulation and process development.
Systems can be supplied for a wide range of different fibre types. These have ranged from corrosive aqueous salt solutions (such as alginate fibres), to acidic systems (such as engineered silk) and also systems using flammable, toxic solvents (such as UHMWPE).
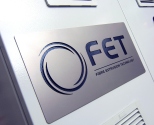
Laboratory and Pilot Bespoke Systems
Bespoke Laboratory and Pilot Equipment for Polymer Extrusion
In recent years, FET has become increasingly focused on the field of hi-tech laboratory and pilot machinery. We excel in finding solutions for challenging projects, working with customers and getting to understand the fine details of what they are seeking to achieve. Our background in providing bespoke extrusion lines for manufacturing systems gives us a broad understanding of processes, configurations and operation – elements that can then be practically applied to pilot and laboratory extrusion equipment.
FET laboratory and pilot bespoke systems
Our Laboratory and Pilot Melt Spinning Extrusion Lines are highly specialised and versatile systems that are designed and built to meet the needs of the most demanding research and development teams in the world. They are supplied as self-contained units for ease of installation in a laboratory and/or small scale process evaluation environment. A variety of options are available:-
- Variety of polymer types
- All combinations of yarn types – UDY, POY, FOY
- Multifilament, Monofilament and Non-Woven versions
- Mono, Bi and Tri-Component technology
- High speed versions up to 6,000 m/m
- High temperature versions
- Corrosion resistant versions for special polymers
- Fully integrated computer control system for data logging, trending and storage
- Equipment for additive dosing of extruded polymers
Applications
FET Laboratory Extrusion Lines are suited to a variety of end uses:
- R&D concept testing
- Product development
- Polymer and additive testing
- Small batch production
- New yarn engineering
- Bio Medical yarns
- Risk elimination
- Additive testing
All extrusion lines allow for a high level of bespoke specification to satisfy exacting laboratory conditions. They are ideal for precision melt spinning of exotic polymers and small batch production for medical device applications
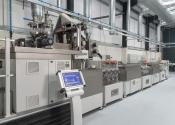
Products and Applications
Systems and Products for specialist markets
FET customers manufacture high value textile materials, in demanding and precise environments. They expect us to provide yarn and fibre engineering knowhow and extrusion equipment which will allow them to consistently produce fibres of the highest quality and to be able to meet required regulatory standards. We excel in the area of specialised novel fibres from exotic and difficult to process polymers.
FET is particularly active in the medical and composites sectors:
Biomedical applications
FET equipment is highly suitable for the development and small volume production of exotic and difficult-to-process biomedical materials, such as resorbable polymers used in medical devices. These include the Engineering Polymers such as PPSU, PEI, PEEK and PC. FET systems are also suitable for processing sustainable polymer types (S-Polyamides, PLA, PHA, S-PET etc.)
FET-100 systems in particular can be specified to be multi-functional, allowing easy and fast conversion between material formats. It configures to all combinations of multifilament, monofilament and melt spinning of nonwoven structures for medical device applications.
Extrusion module options include multi-polymer capability, bi-component, tri-component and can be specified for high temperature capability and corrosion resistant construction. The bi-component systems are ideally suitable for yarn engineering and particularly in sheath core format. This facilitates the inclusion of functional materials into the polymer matrix.
Composite applications
FET systems are used in the development and small volume production of pre-cursor synthetic textile materials used in the manufacture of high performance composites.
They are capable of working with exotic and difficult-to-process polymers which are frequently those used in composite structures. These include so-called “engineering polymers” such as PPSU, PEI, PEEK and PC Polycarbonates. FET systems are also suitable for processing sustainable polymer types (S-Polyamides, PLA, PHA, S-Pet etc), which means they are ideal for the production of bio-degradable composite materials.
Systems configure to all combinations of multifilament, monofilament and melt spinning of nonwoven structures as required. A particular speciality can be found in melt blowing viscous materials into nonwoven web structures for use as composite veils.
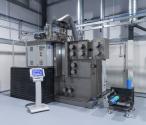
FET-100 Series
Multi-Functional Laboratory Pilot Melt Spinning Systems
A significant feature is that FET-100 systems can be specified to be multi-functional, allowing for easy and fast conversion between material formats. It configures to all combinations of multifilament, monofilament and melt spinning of nonwoven structures as required.
This highly versatile and flexible system is ideal for research and development, designed specifically for detailed investigation into extruded textile materials. The FET-100 Series comprises the following modules:
FET-100 Extrusion
Central to all FET laboratory and pilot melt spinning systems is the specially developed extrusion module, the FET-100 Extrusion which allows multiple process options. This extrusion module is designed to provide melt spinning capacity to any one of the three downstream process options. The module is mounted on a hydraulic lifting table which permits automated adjustment of the working height
FET-101 Multifilament
FET offers a wide range of bespoke pilot and laboratory melt spinning systems for continuous multifilament applications capable of matching the demands of all users. Each variation of the FET-101 Multifilament option is uniquely specified and designed for world leading companies and research institutes for a wide variety of applications.
FET-102 Nonwoven
Simple integration of the FET-102 Nonwoven option gives the possibility of melt spinning nonwoven materials. Melt blown and spun bond types can both be achieved on the same base system. This is applicable to a broad range of polymers, including viscous materials normally not appropriate for the melt blowing or spun bond process. Applications include resorbable biomedical polymers and engineering grade materials.
FET-103 Monofilament
Utilising the same extrusion module, FET can also provide specialist laboratory and pilot melt spinning systems for monofilament applications, the FET-100 monofilament. As with multifilament equipment, our flexible monofilament systems are being used by high tech organisations and research institutes on a variety of technical and R&D projects
Benefits include substantial savings on cost, floor space and also the ability to add optional equipment in the future. Extrusion module options include multi-polymer capability, bi-component and tri-component and can be specified for high temperature capability and corrosion resistant construction.
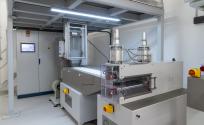
Spunbond Nonwoven Systems
FET Spunbond Nonwoven systems
Although the processes share some similarities, the spunbond process uses different techniques to form the filaments compared to meltblown. In the FET spunbond process, high velocity air jets are used to melt draw continuous filaments and to distribute uniform, random array onto the vacuum conveyor. The outcome is that Spunbond webs are typically stronger than their meltblown counterparts. This is due to the Spunbond fibres being generally thicker and having a higher degree of molecular orientation.
Benefits of Spunbond technology
These properties of Spunbond nonwovens provide a number of benefits:
- Tensile strength
- Abrasion Resistance
- Minimal fibre shedding
Spunbond nonwovens are widely utilised by various industries, especially the medical, personal care and hygiene sectors, as an affordable disposable alternative to traditional textiles. Spunbond nonwovens are widely utilised by various industries, from geotextiles to medical devices. They are often employed in combination with meltblown webs to form multilayer laminates that produce high performance fabrics.
Composite Nonwoven Systems
Meltblown and spunbond have different diameter filaments and other property variations. When the two processes are combined, this allows a multitude of technical benefits to be achieved. Meltblown / Spunbond multilayer fabrics include SM (spunbond-meltblown) and SMS (spunbond-meltblown-spunbond), which are frequently used in filtration applications.
Composite nonwovens have the advantage of flexibility to bond with other types of webs, resisting shedding, with relatively higher mechanical strength, and are stable and resilient. They also have the advantage of forming functional fibres, such as antibacterial, and receiving permanent treatment (eg, flame retardancy) at the fibre extrusion stage.
FET’s composite nonwoven systems are proven to provide solutions for nonwovens manufacturers and research establishments globally.